Fuel Cells
Fuel Cells
- Hydrogen has been used in petroleum refining and steel manufacturing processes and was produced by reforming petroleum fuels or separating and refining from steel mills.
- There are high expectations for water electrolysis using renewable energy, NH3 (ammonia) reforming, and biomass-derived hydrogen in recent years.
- We, Nikki-Universal, offer a wide variety of catalysts used in fuel cells.
- More than ten years have already passed since PEFC (Polymer Electrolyte Fuel Cell) and SOFC (Solid Oxide Fuel Cell) were launched.
- Since the sulfur content in city gas is a catalyst poison for reforming and shifting catalysts, PEFC needs an appropriate desulfurization agent.
- Firstly, steam reforming reacts in the temperature range of 700℃ or higher, and the CO contained in the syngas is converted to hydrogen by the shift catalyst. Finally, the CO after the shift catalyst is removed by the PROX catalyst.
- In SOFC, there is no hydrogen purification system like in PEFC, but hydrogen and carbon monoxide are converted in the cell stack after reforming. Then, the supplied oxygen reacts with the hydrogen and carbon monoxide to form water vapor and carbon dioxide while at the same time releasing electrons to process the CO completely and exhaust it.
De-Sulferization
- Conventional hydrodesulfurization catalyst used in refineries uses hydrogen to decompose and remove impurities such as sulfur, nitrogen, and oxygen. However, organic sulfur compounds used in city gas odor affect the reforming catalyst in residential, commercial, and industrial fuel cells. Therefore, we use catalysts and adsorbents to remove organic sulfur compounds in advance.
- If the propane gas is being used, organic sulfur compounds and inorganic sulfur compounds need to be removed, and we have to remove a wide variety of sulfur compounds.
- We have a wide range of catalysts (hydrogenated desulfurization catalysts) and adsorbents to meet sulfur removal needs in various fields, such as hydrogen fuel cells and biomass-derived energy utilization.
- We will propose the most suitable catalyst or adsorbent if you provide conditions such as sulfur species, temperature, moisture, etc.
The adsorption performance of COS (carbonyl sulfide) is as follows.
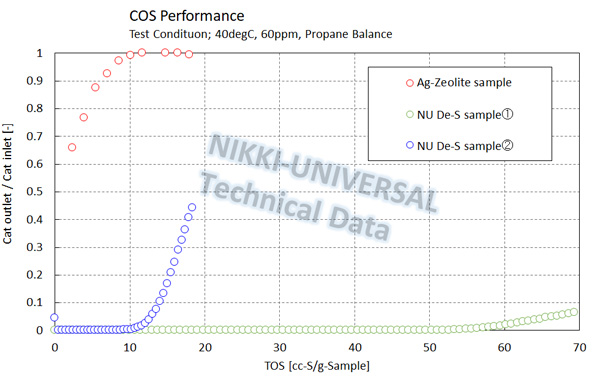
The adsorption performance of DMS (Dimethyl Sulfide) is as follows.
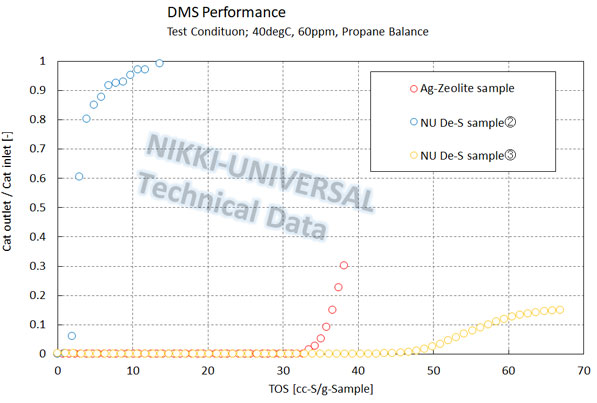
About Adsorption Characteristics
- Influence of gas conditions
The adsorption capacity varies depending on the gas type, such as TBM (tert-butyl Mercaptan), COS (carbonyl sulfide), and DMS (dimethyl sulfide)., temperature, and moisture content.
We can meet the sulfur removal needs of our customers by combining adsorbents and catalysts suitable for a wide variety of gases.
The adsorption performance of COS (carbonyl sulfide) with high-temperature operation is as follows.
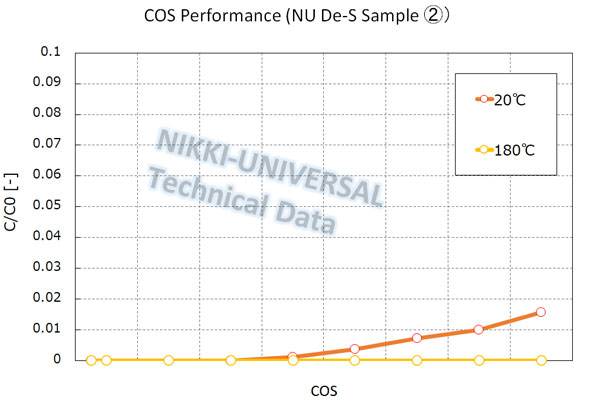
The adsorption performance of DMS (Dimethyl Sulfide) is as follows.
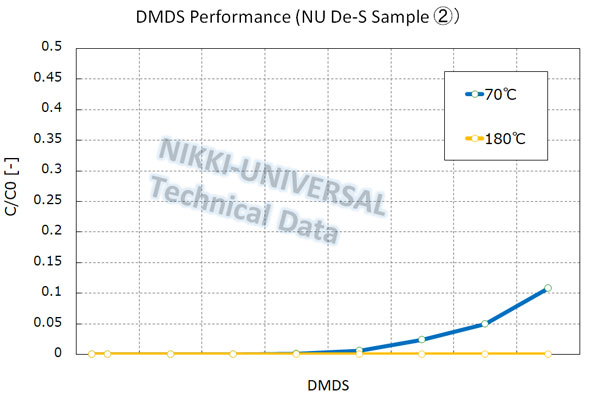
Steam Reforming Catalyst
- We offer Ru, Rh, and Ni-based reforming catalysts for methane and propane and kerosene reforming catalysts.
- In addition, there is a growing need for improving from ammonia as we move toward a clean, low-carbon society.
- CO shift catalyst (WGS)
- CO selective oxidation catalyst (PROX)
We handle precious metal-based reforming catalysts that have good performance under low-temperature.
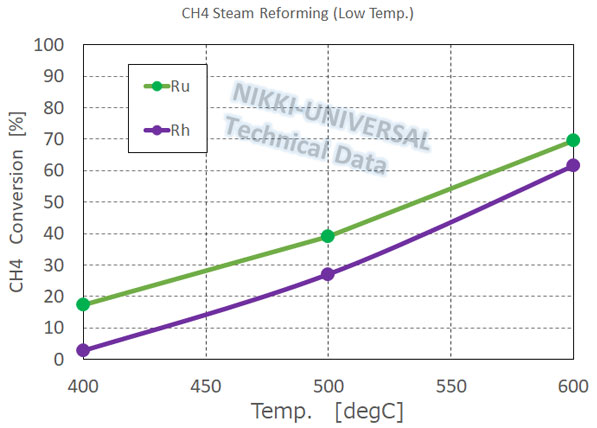
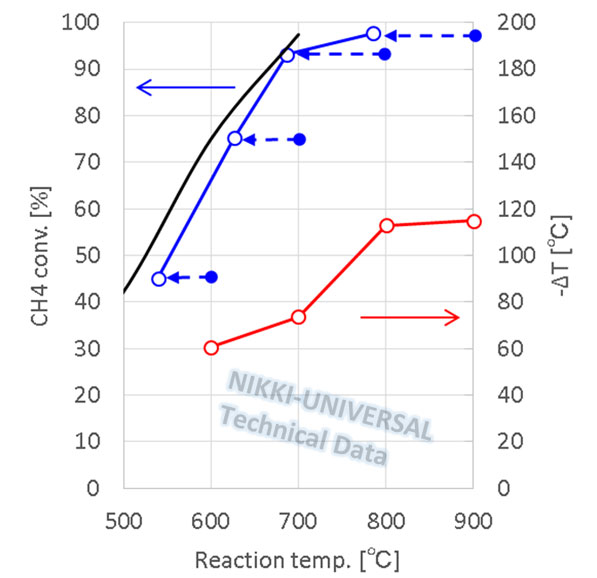
CO Shift Catalyst
- In polymer electrolyte fuel cells(PEFC), carbon monoxide is a byproduct of the steam reforming of hydrocarbons to produce hydrogen. Since carbon monoxide corrodes the electrodes, it is necessary to remove CO.
- The water-gas shift reaction(WGS) (CO + H2O = CO2 + H2) consumes CO and produces hydrogen.
PROX Catalyst
- We provide PROX catalysts to remove CO that could not be fully reacted by the aqueous gas shift described above.
Contact Sales Department
Department | Business Innovation Office |
---|---|
Contact Form | |
TEL | 81-3-5436-8484 |
FAX | 81-3-5436-8680 |